Ready Meals
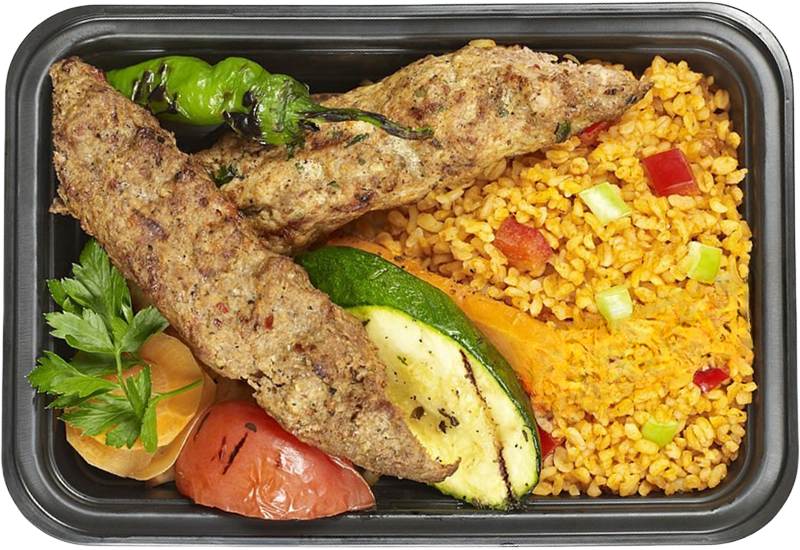
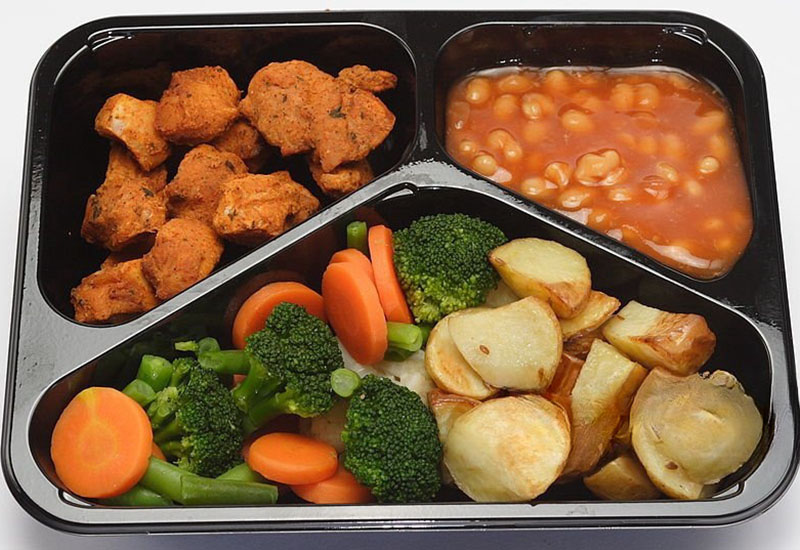
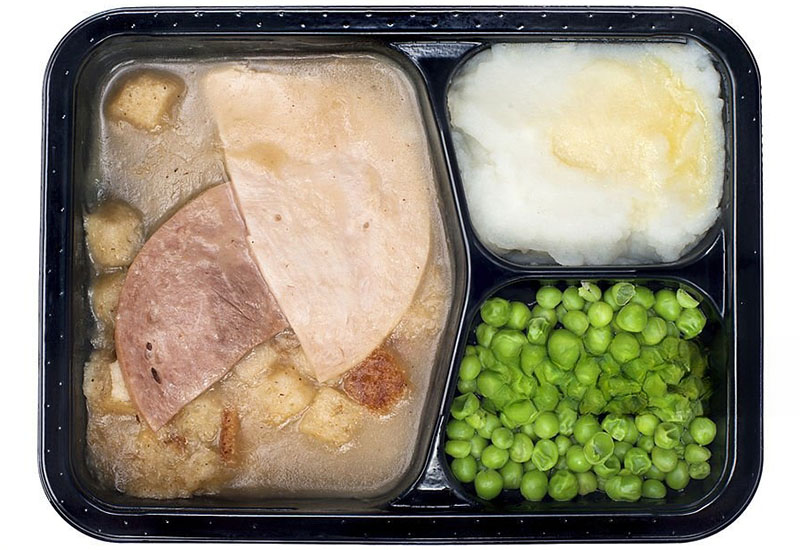
Fully Automated Tray-Packaged Ready Meal Production Line
Background
With the accelerating pace of modern life, the market for ready meals has grown steadily, driven especially by consumer demand for convenience and quick consumption. In response to client requirements for high-quality, long-shelf-life ready meals, the Resure team has established a project group to design a fully automated portioning and sealing packaging solution for ready meal production.
The main objectives of this project are to design and implement a tray-packaged ready meal production line that meets the following needs:
- Precise Portioning and Ingredient Variety: Ready meals typically include main dishes, side dishes, sauces, etc., with different portioning requirements for each. The line requires multiple measuring devices to accurately control the dispensing of each component, ensuring product consistency.
- Food Safety and Freshness: To ensure extended shelf life and food safety, the sealing phase of the line will incorporate a Modified Atmosphere Packaging (MAP) system, infusing nitrogen or carbon dioxide to inhibit microbial growth and extend product freshness.
- Automation and Efficiency Enhancement: A PLC control system will be adopted to automate tray handling, portioning, sealing, and inspection, minimizing manual involvement and boosting both production efficiency and product uniformity.
- Quality Control and Error Prevention: The line will be equipped with weight checkers, metal detectors, and an intelligent alarm system to ensure each product meets quality standards, with defective items automatically removed.
This project will enable the client to deliver ready meals with stable quality and well-crafted packaging, meeting consumer demands for convenience, health, and hygiene, and strengthening brand competitiveness.
Solution Design
1. Overview
This project design centers around efficiency, precision, and safety, aiming to establish a fully automated tray-packaged ready meal production line. The line automates the entire process—from raw ingredient dispensing, filling, and ingredient mixing to sealing packaging—ensuring consistency in product portions and ingredients while extending product freshness.
- Key Technical Choices:The production line incorporates precise multi-head weighing systems, measuring cup liquid filling machine and counting automatic loading and unloading device to achieve accurate portioning of all raw ingredients and seasonings. A Modified Atmosphere Packaging (MAP) module is included for freshness preservation before sealing, extending the product shelf life.
- Production Mode: The entire line is interconnected through a PLC control system to reduce manual intervention. The HMI touchscreen is used for monitoring and managing production line data, while the intelligent detection module ensures that each product meets quality standards.
Packaging Process | Designed to meet production capacity requirements, the line features a continuous four-station chain and pusher mixed packaging system. |
Tray Dimensions | Tray: 187 x 137 mm (height: 30-50 mm) Bowl: 150 mm (height: 35-55 mm) |
Temperature | 3℃-60℃ |
2. Equipment Structure
This project is divided into two main sections:
Section One — Push-Rod Conveyor Line
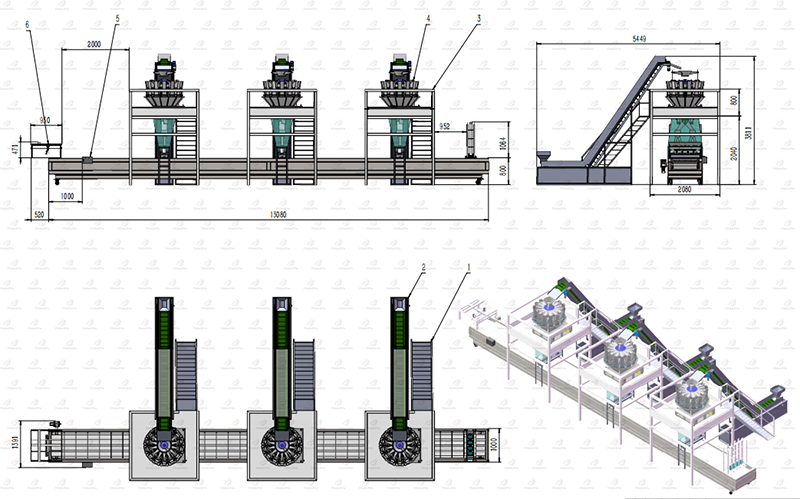
The conveyor line consists of 6 basic modules:
- Tray feeding mechanism
- Push-rod conveyor system
- 3 sets of multihead weigher
- Reserved workstations
- Electrical box
- Tray gripper mechanism
The tray feeding mechanism automatically places the trays on the conveyor system, which then transports them to the designated workstations in a timed and orderly manner. The three sets of multihead weigher are responsible for automatic feeding, and the gripper transfer mechanism places the trays with materials onto the subsequent chain conveyor system.
Second Section — Chain Plate Conveyor Line
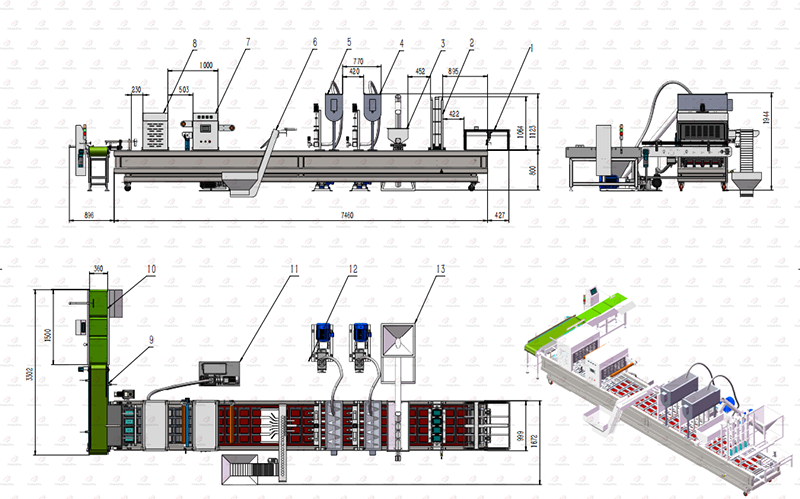
In this section, various liquids and pastes are filled, along with the placement of irregularly shaped and countable items such as small patties and meatballs. This is followed by vacuum sealing, gas flushing, sealing, and secondary sealing reinforcement. After sealing, the trays are pushed onto the conveyor belt and sent to the weighing machine. If any products are underweight, the system will automatically reject them.
3. Features
- The system can be programmed to follow predetermined recipes, controlling different feeding stations to dispense ingredients according to set portions. Adopting the SMED (Single Minute Exchange of Dies) approach for quick mold change enables fully automated one-touch settings, significantly reducing the preparation time required for product changeover. This is particularly suitable for food processing packaging lines that handle multiple materials, varieties, and small batch production.
- The system utilizes the most advanced intelligent thermal transfer technology, significantly reducing ribbon waste and saving at least 20% on consumables compared to similar products. Ribbon replacement is quicker, reducing downtime. It can directly print recipe lists, barcodes, and other information on laminated films, preventing food safety issues such as ink penetration that may occur with traditional inkjet printing.
- All feeding stations are equipped with material quantity monitoring systems. When the material level falls below the set threshold, an alarm is triggered to notify operators to replenish the material, preventing production line downtime. If any feeding station runs out of material, the system will automatically halt the production line to avoid the production of defective products.
- The equipment includes a 2-2.5 meter reserved position, allowing for additional manual feeding processes to address unexpected material supply issues. The reserved position is equipped with control power and 9-pin control signal interfaces, making it easy to add new feeding systems and expand capacity in the future.
- The systemhas undergone structural improvements to meet cleanliness and hygiene requirements. The program settings include a manual forced material-clearing mode to ensure efficient cleaning of the equipment.
- The system features IoT remote communication capabilities for rapid fault diagnosis, offering 24-hour remote support to quickly guide customers in troubleshooting and resolving issues.
4. Equipment Configuration
(1)Automatic Tray Dropping Device
- Precisely places trays onto the conveyor belt, ensuring stability during transport and providing supportfor the material feeding and filling processes.
(2)Multihead Weigher Accurate Weight Automatic Loading and Unloading System
- Multihead weigher for accurate weighing of bulk ingredients (e.g., rice, main courses) to minimize errors in material feeding.
- The number of multihead weighers can be adjusted based on the recipe requirements.
(3)Tray Gripper Feeding Device
- Uses a mechanical gripping device to ensure precise tray positioning on the conveyor belt, enabling seamless transfer between workstations and improving overall line stability.
(4)Measuring Cup Solid Filling Machine
- Fills trays with main ingredients, such as fried noodles or rice, according to the preset amount, ensuring consistency in portion size and product specifications.
(5)Measuring Cup Liquid Filling Machine
- For precise filling of sauces and other liquid seasonings, equipped with anti-drip devices to ensure accurate liquid filling in trays.
(6)Counting Automatic Loading and Unloading Device
- Used to accurately portion ingredients like meatballs, patties, fried eggs, or boiled eggs. The intelligent counting and gripping system ensures consistent portioning and prevents breakage.
(7)Tray Sealing Machine
- Automatically covers the trays with films and applies heat sealing and modified atmosphere packaging (MAP). Nitrogen or carbon dioxide is introduced to extend shelf life.
(8)Weight Checker
- Used to check the total weight of each tray to ensure it meets quality standards. Non-conforming products are automatically rejected.
(9)Metal Detector
- Detects metal contaminants in the products to ensure food safety, automatically removing any non-conforming products.
(10)Flat Labeling Machine
- Applies labels to the surface of trays or films, indicating production dates, batch numbers, and barcode information for product traceability and management.
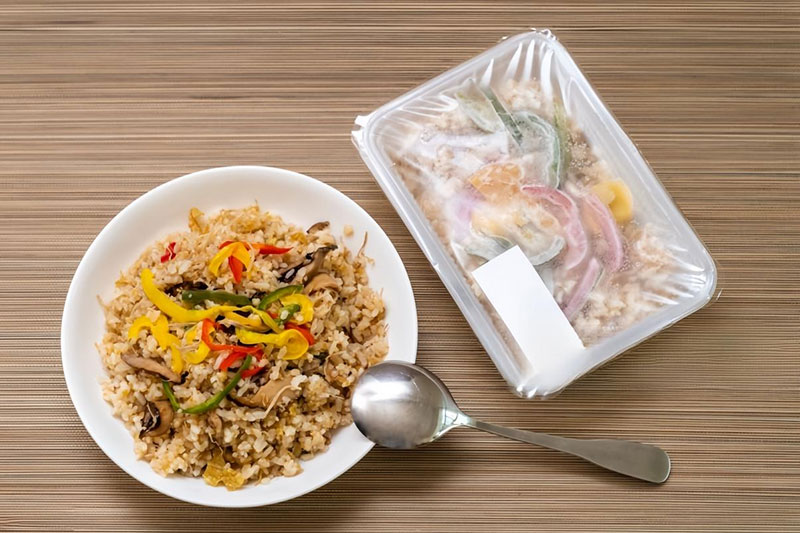
Practical Application
Product Ingredients: Boiled potato slices, Cooked diced meat, Boiled vegetable mixture, Meat and vegetable soup